回路設計が終わったらブレッドボードで動作確認したりしてからプリント基板を作るかユニバーサル基板で作るかになりますよね。
表面実装部品を多用する時にはユニバーサル基板でも力業で作れない事はないですがやはりプリント基板を作ってしまうのが仕上がりも綺麗で信頼度も高くなりますね。
今回は私が自作のプリント基板を生基板から作っている方法をご紹介したいと思います。
プリント基板の種類
外注のプリント基板ではなく自作基板として考えると、制作方法は結構あります。
1.感光液を塗布する方法
私が主に制作している方法になります。
生基板に感光液を塗布して乾燥させてから感光します。
やり方については後述します。
2.レーザープリンタを使用する方法
レーザープリンタのトナーを利用する方法です。
用紙に印刷されたパターンを水で濡らしてからアイロンを使用して生基板に転写します。
この方法では感光+現像のプロセスがないので工程短縮になりますが私が試した時には綺麗に転写出来ない部分などがあって実用には至りませんでした。
3.専用のアイロンプリント用紙を使用する方法
耐熱性の専用フィルムにレーザープリンタで印刷してからアイロンで転写します。
細かいパターンの仕上がりは悪くなかったのですが、力加減で転写ムラが出てしまいました。
もう少し練習すれば綺麗に転写できると思いますがフィルムの入手が簡単ではなく使わなくなってしまいました。
4.CNC加工機を使用する方法
CNCリューターを利用して基板の銅箔を薄く削ってパターンを作る方法です。
私自身CNCリューターを持っていませんので試せいませんが0.5ミリピッチのパターンが作れるなら十分実用になりそうです。
5.市販の感光基板を使用する方法
サンハヤトのポジ感光基板が一番メジャー感光基板になります
感光液の塗膜も均一で感光に失敗しなければ非常にきれいなパターンが形成できます。
サンハヤトでは厚みやサイズ更に基板の基材も多種揃っていてフィルム基板も揃っています。
現在ではサンハヤトのポジ感光基板と自前で塗布する基板を使い分けているのですがどちらかというと自前で塗布する方が多いです。
何よりポジ感光基板の感光を失敗した場合その基板は使い道がなくなってしまいますが自前で塗布出来るといくらでもやり直しが出来るので長期的にみると無駄がなくて良いです。
6.アセトンを使用した転写
100均などで購入できる除光液を使用した転写方式です。
レーザープリンタで印刷をしたパターンを生基板に転写するという部分では、アイロンを使ったトナー転写に近いです。
大きな違いはアイロンを使わず除光液のみで転写できる為、お手軽に作れるところでしょうか。
不安材料としては両面基板が問題なく作れるかどうかです。OHPシートの様な透明なフィルムなら位置合わせも簡単ですがPPC用紙でどこまで正確に位置合わせが出来るかが難しそうです。
片面づつ転写することになりますから、既に転写が済んでいる側にアセトンが回り込むとパターン切れになる危険も考えて作業する必要がありそうです。
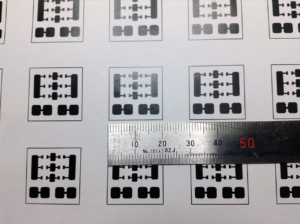
7.ドライフィルムを使用する方法
感光剤が塗布されたフィルムを生基板に熱転写して感光基板を作る方法で、アイロンや市販のラミネーターを使って転写します。
感光基板を作るフィルムですからその後は感光、現像、エッチング工程が入ります。
感光液を塗布して自作基板を作る
自作基板で使用している基板サイズは100 x 100を使っています。
それ以上大きいものが必要な時はサンハヤトの基板を使うなどしています。
使用している感光液、シンナー、現像液はこちらです。
富士薬品 ポジ型フォトレジスト FPPR-200
富士薬品 ポジ型フォトレジスト専用シンナー
富士薬品 ポジ型フォトレジスト専用現像液
自作基板の手順は以下になります。
1.生基板を磨いて汚れや油を洗い落とす
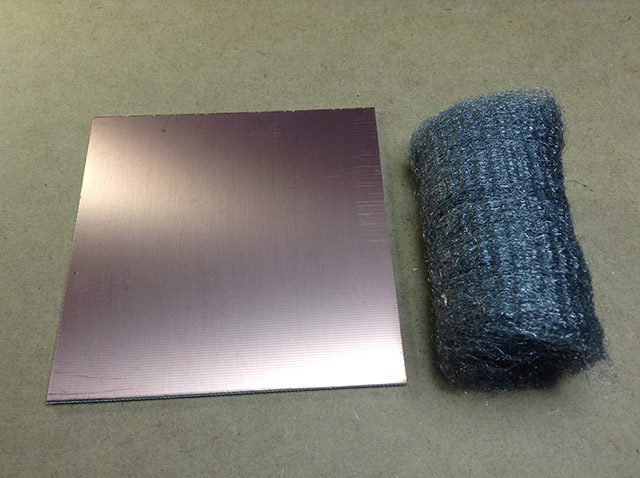
洗剤的なものは使わず流水しながらスチールウールでしっかり磨きます。
ここでしっかり磨けていないと後々現像液を弾いて失敗します。
2.水分を拭き取ったら専用シンナーで拭いて綺麗にする
ある程度水気を拭いたらドライヤーでしっかり乾燥させます。
そして残った油分を完全に取る為と現像液の伸びを良くするため専用シンナーで拭きます。
これ以降、銅箔部分に油分が付くと失敗の元なので直接触れないように注意します。
3.感光液を出来るだけ紫外線に晒さない様、部屋を出来るだけ暗くする
部屋の蛍光灯くらいではすぐに影響が出る訳ではありませんが、少しでも回数を重ねれば少なからず影響が出てくる事が考えられるので手元が見える程度には暗くしてあげます。
4.自作冶具に両面テープを小さく貼り、そこへ生基板を貼り付ける
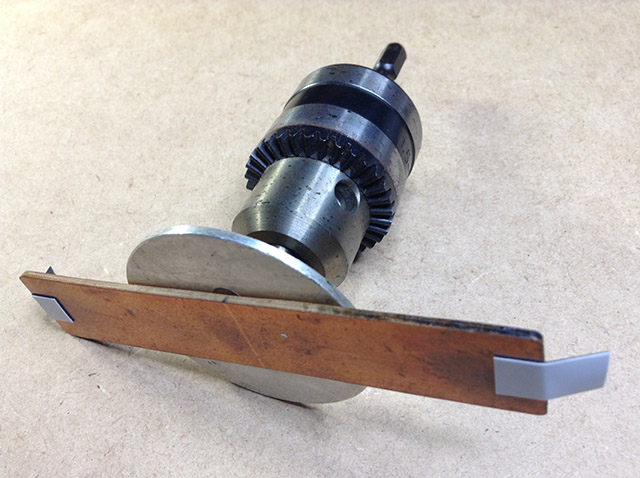
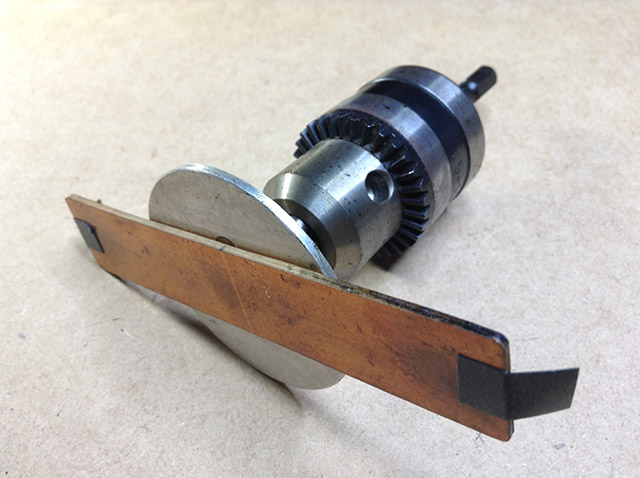
片面基板なら余り気にせず貼っても問題ないですが両面基板の場合、感光剤塗布面に貼る事になるので接着面が大きすぎると剥すのに苦労しますし、塗布面が剥がれる恐れがあるので注意します。
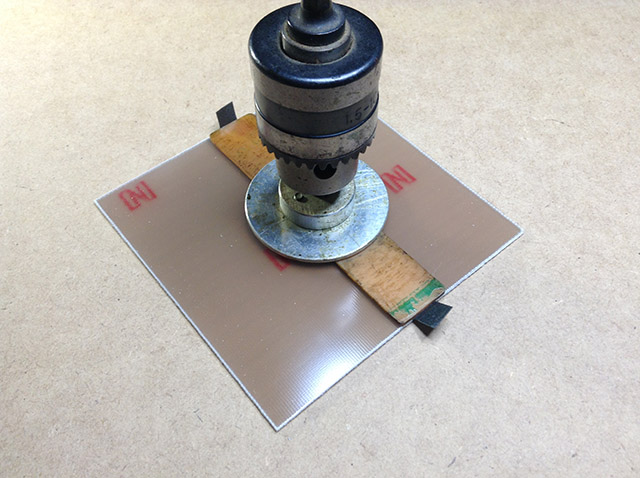
5.冶具を電動ドリルに取り付け基板へストローを使い感光液を滴下して塗り広げる
基板を上に向けた状態で感光液を中心に滴下してストローの側面を使って軽く塗り広げます。
ストロー以外にも100均で手に入るシリンジなども使えますが、使用後に綺麗に洗浄する必要がありシンナーを使う事で無駄と手間が増えますので安価で手に入るストローを使っています。
結構アバウトに塗り広げても問題ないですが、端の方へや広げない方が無難です。
端まで塗り広げた時、両面基板の場合反対側へ垂れてしまう事があるので注意します。
6.素早く基板を下に向けバケツの中でドリルを回転させて余分な感光液を飛ばす
ドリルを回転させた遠心力を利用して過剰な感光液を飛ばします。
上向きのまま回転させてしまうと部屋が大変な事になるので、洗面器やバケツを使うと良いです。
ここでどれくらいの速度でどれだけ回転させるかはドリルの性能で大きく変わるので何回か試してコツを掴みましょう。やり直しが何度でも出来るのも強みですので。
7.10秒ほど回転させたら素早く基板を上に向けドライヤーでべたつきがなくなる程度に強制乾燥させる
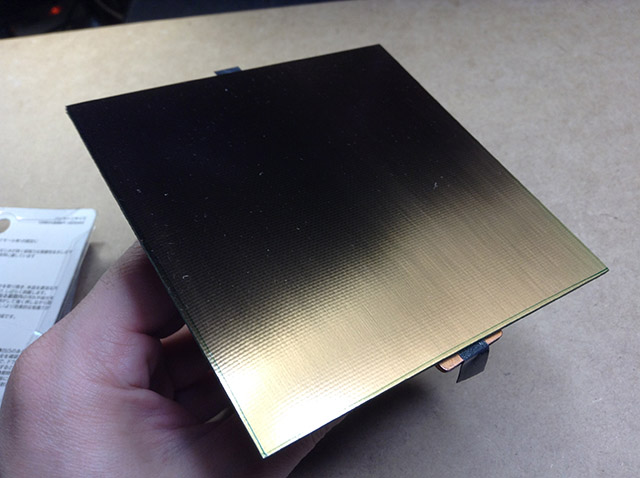
そろそろかな?というくらいになったら回転させながらドライヤーを当て始め余熱を掛けておきます。
回転を止めたら間髪を入れずに感光液を乾燥させます。
ここで手間取ると端に溜まっている感光液が中心へ向かって戻ってくるので出来るだけ早く乾燥させます。
8.両面基板の場合4番へ戻って同じ作業をする
本来なら塗布後はベーク(乾燥)工程を入れると良いらしいです。
初期の頃はドライヤーで15分程度熱風を当てていましたが、現在は特にやらなくても綺麗に現像できています。
気になる場合はベーク工程を入れると感光液の硬度が増して扱いやすいと思います。
両面基板1枚を塗布するのに5分も掛からず出来ますので準備と片付けの方が時間が掛かるかもしれません。
ですので基板を制作する時は数枚余分に作っておくと良いと思います。
まとめ
以前と比べてプリント基板の外注の敷居はかなり下がっています。
一番のネックだったのがイニシャル費用が高いという部分でしたが現在はイニシャル費用が掛からないところもありかなり安く作る事も出来ます。
ただやはり外注すると仕上がりは良いですが、1枚ものやすぐ作りたいという場合には自分で作れるとかなり便利かと思います。
自作基板だと表面実装部品の下にビアが入れ難い等不便もありますが自分用にちょこっと作りたいという時には大変便利だと思います。